PPAP Production Part Approval Process Guide
This file outlines the requirements for the PPAP process, critical for quality assurance in manufacturing. It provides a comprehensive list of necessary documentation and approvals. Understanding this process ensures compliance and efficiency in production.
Edit, Download, and Sign the PPAP Production Part Approval Process Guide
Form
eSign
Add Annotation
Share Form
How do I fill this out?
To complete this form, carefully review all required elements listed in the guidelines. Gather the necessary documentation, ensuring each piece is accurate and up-to-date. Once all items are compiled, follow the submission instructions to send your form.
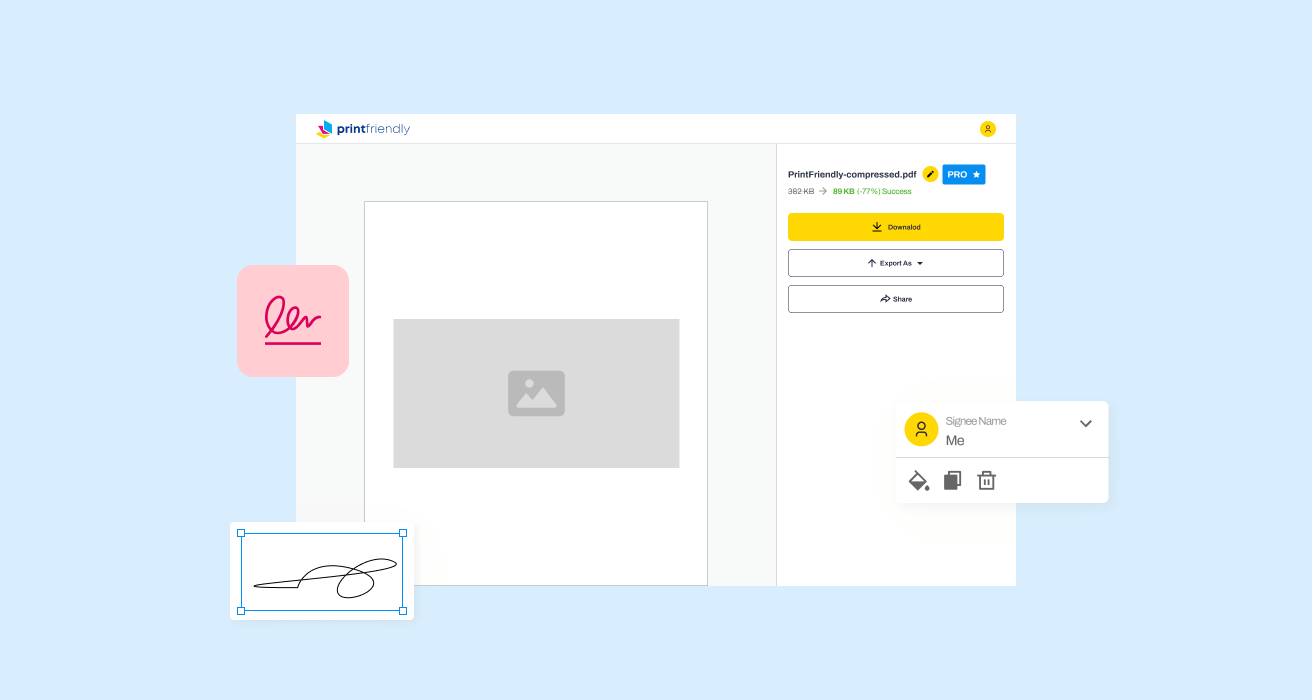
How to fill out the PPAP Production Part Approval Process Guide?
1
Review the 18 PPAP elements carefully.
2
Compile all required documentation according to the checklist.
3
Ensure all signatures and approvals are obtained.
4
Verify that everything is accurate and complete.
5
Submit the compiled documents in the specified format.
Who needs the PPAP Production Part Approval Process Guide?
1
Manufacturers needing to ensure product quality.
2
OEMs verifying supplier compliance.
3
Quality assurance teams auditing production standards.
4
Suppliers providing parts for automotive products.
5
Engineers needing to document design approvals.
How PrintFriendly Works
At PrintFriendly.com, you can edit, sign, share, and download the PPAP Production Part Approval Process Guide along with hundreds of thousands of other documents. Our platform helps you seamlessly edit PDFs and other documents online. You can edit our large library of pre-existing files and upload your own documents. Managing PDFs has never been easier.
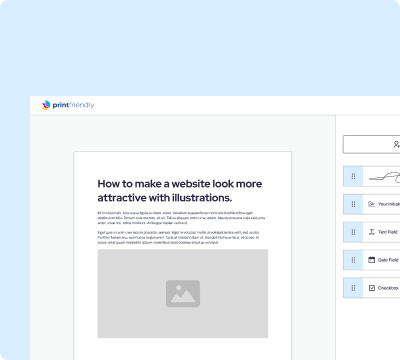
Edit your PPAP Production Part Approval Process Guide online.
Editing your PPAP PDF on PrintFriendly is simple and efficient. Start by uploading your document to our platform. Utilize our intuitive tools to make necessary changes and annotations effortlessly.
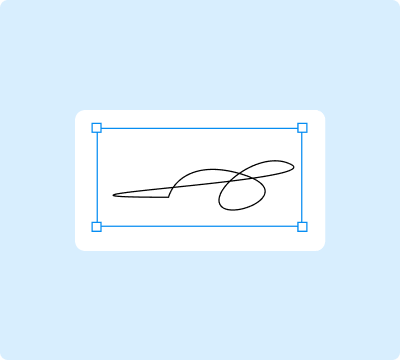
Add your legally-binding signature.
You can sign your PDF directly on PrintFriendly with ease. Our platform allows you to add an electronic signature in just a few clicks. Ensure your document is officially approved without the hassle of printing.
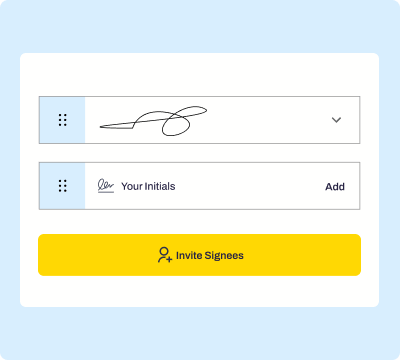
Share your form instantly.
Sharing your PDF is seamless on PrintFriendly. Use our share tools to distribute your document via email or social media. Collaborate with your team effortlessly by providing them direct access to the edited file.
How do I edit the PPAP Production Part Approval Process Guide online?
Editing your PPAP PDF on PrintFriendly is simple and efficient. Start by uploading your document to our platform. Utilize our intuitive tools to make necessary changes and annotations effortlessly.
1
Upload your PDF document to PrintFriendly.
2
Use the editing tools to make changes as needed.
3
Add annotations or comments where necessary.
4
Review all changes to ensure accuracy.
5
Download the edited document for your records.
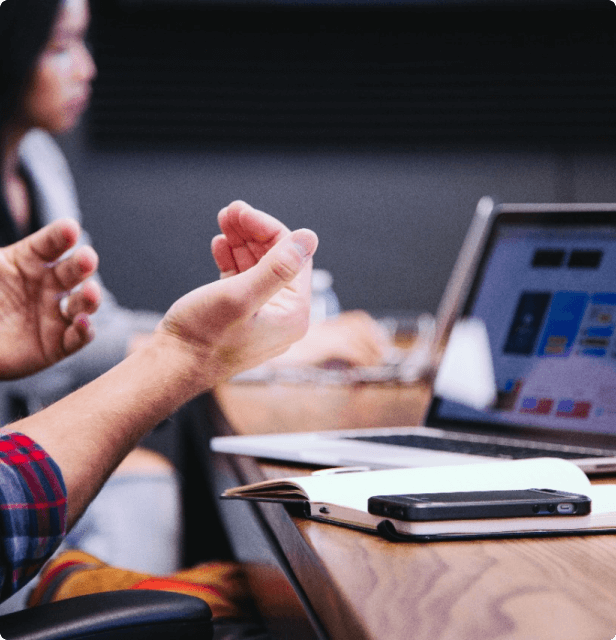
What are the important dates for this form in 2024 and 2025?
For 2024 and 2025, ensure timely submission of PPAPs according to OEM schedules. Check for specific deadlines set by individual OEMs as dates may vary based on production cycles and contracts.
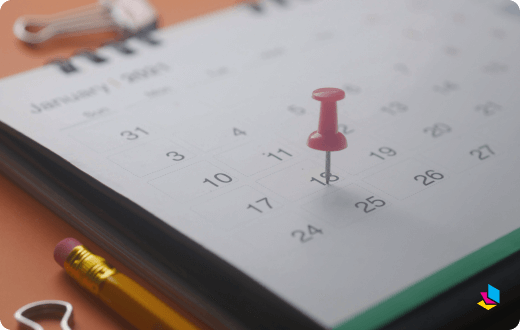
What is the purpose of this form?
The purpose of the PPAP form is to document the compliance with quality standards required in the automotive industry. It ensures that all components meet customer specifications before production begins. This promotes collaboration between suppliers and OEMs, reducing the risk of defects and enhancing the overall quality of products.
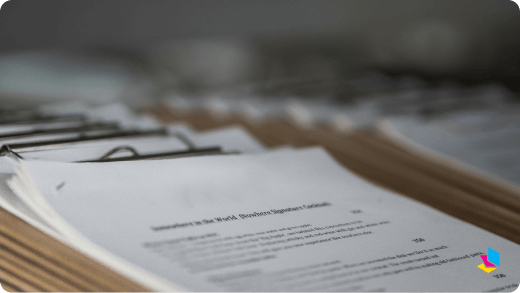
Tell me about this form and its components and fields line-by-line.

- 1. Design Records: Includes part drawings needed for approval.
- 2. Engineering Change Documents: Documentation of changes incorporated into the design.
- 3. Engineering Approval: Signatures or agreements from engineering teams.
- 4. Design FMEA: Failure Mode and Effects Analysis to ensure design integrity.
- 5. Process Flow Diagram: Visual representation of the manufacturing process.
- 6. Process FMEA: Analysis focused on the production process for potential failure.
- 7. Control Plan: Plans detailing control measures both pre-launch and during production.
- 8. MSA Studies: Measurement System Analysis that validates the reliability of measurement systems.
- 9. Dimensional Analysis: Analysis of dimensions through sample measurements.
- 10. Material / Performance Test Result: Results from material testing to confirm specifications.
- 11. Initial Process Studies: Preliminary studies to verify process capabilities.
- 12. Qualified Lab Documents: Documents proving lab qualifications and testing accuracy.
- 13. AAR: Appearance Approval Report to validate aesthetics.
- 14. Sample Product: Physical sample produced for customer evaluation.
- 15. Master Sample: Reference sample for future production runs.
- 16. Checking Aids: Tools or methods employed to verify compliance.
- 17. Customer Specific Requirements: Any unique specifications provided by the customer.
- 18. PSW: Part Submission Warrant indicating submission approval.
What happens if I fail to submit this form?
Failure to submit the PPAP form may result in delayed approvals and potential impacts on production schedules. Additionally, it could lead to non-compliance with customer requirements, resulting in penalties or rejections. It is crucial to follow submission guidelines to ensure smooth processing.
- Production Delays: Missing documents can hold up production processes.
- Quality Issues: Non-compliance may lead to defective products.
- Financial Penalties: Late submissions could incur additional costs.
- Reputational Damage: Failure to adhere to standards affects supplier reputations.
- Contract Violations: Not following PPAP can breach agreements with OEMs.
How do I know when to use this form?
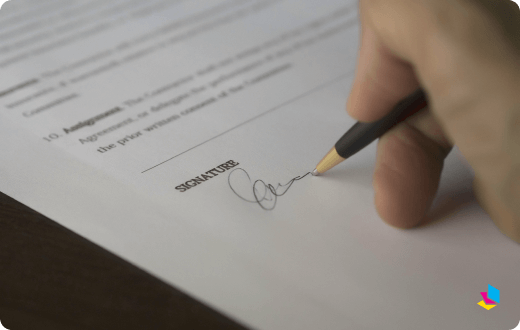
- 1. New Product Development: Required for initial part approval before mass production.
- 2. Changes to Existing Parts: To document any modifications made to already approved parts.
- 3. Supplier Audits: Necessary for audits to validate supplier compliance.
- 4. OEM Requirements: Must be filled for OEMs to assess product quality.
- 5. Regulatory Compliance: To meet industry standards and regulations.
Frequently Asked Questions
What is a PPAP?
PPAP stands for Production Part Approval Process, ensuring that suppliers meet manufacturing quality standards.
How do I begin filling out the PPAP?
Start by reviewing the required elements and gathering all necessary documentation.
Can I edit my PDF on PrintFriendly?
Yes, you can easily edit your PDF using our intuitive editing tools directly on PrintFriendly.
Is a signature required on the PPAP?
Yes, an official signature is necessary to validate the document before submission.
Can I share my PPAP after editing?
Absolutely! PrintFriendly allows you to share your PDF via email or social media.
What happens after I submit the PPAP?
You will receive communication regarding your approval through the signed PSW.
How do I know if my PPAP is approved?
Approval is communicated upon receipt of the signed Part Submission Warrant (PSW).
What if I forget to include a document?
Ensure to check the checklist before submission to avoid missing any necessary documents.
Where can I find the PPAP requirements?
Refer to the official PPAP guidelines for your industry or consult with your OEM.
Can I print my PPAP after editing?
Yes, after editing, you can download and print your finalized PPAP document.