Implement Total Productive Maintenance (TPM) in Manufacturing Industry
This file discusses the implementation of Total Productive Maintenance (TPM) to reduce machine breakdowns and improve productivity. It includes a literature review, case study, and analysis of the effectiveness of TPM. The focus is on autonomous maintenance, planned maintenance, and overall equipment effectiveness.
Edit, Download, and Sign the Implement Total Productive Maintenance (TPM) in Manufacturing Industry
Form
eSign
Add Annotation
Share Form
How do I fill this out?
This section provides instructions on how to complete the content of this file. It outlines the steps necessary to implement Total Productive Maintenance (TPM) in a manufacturing unit. Follow the detailed instructions to ensure proper application of TPM concepts.
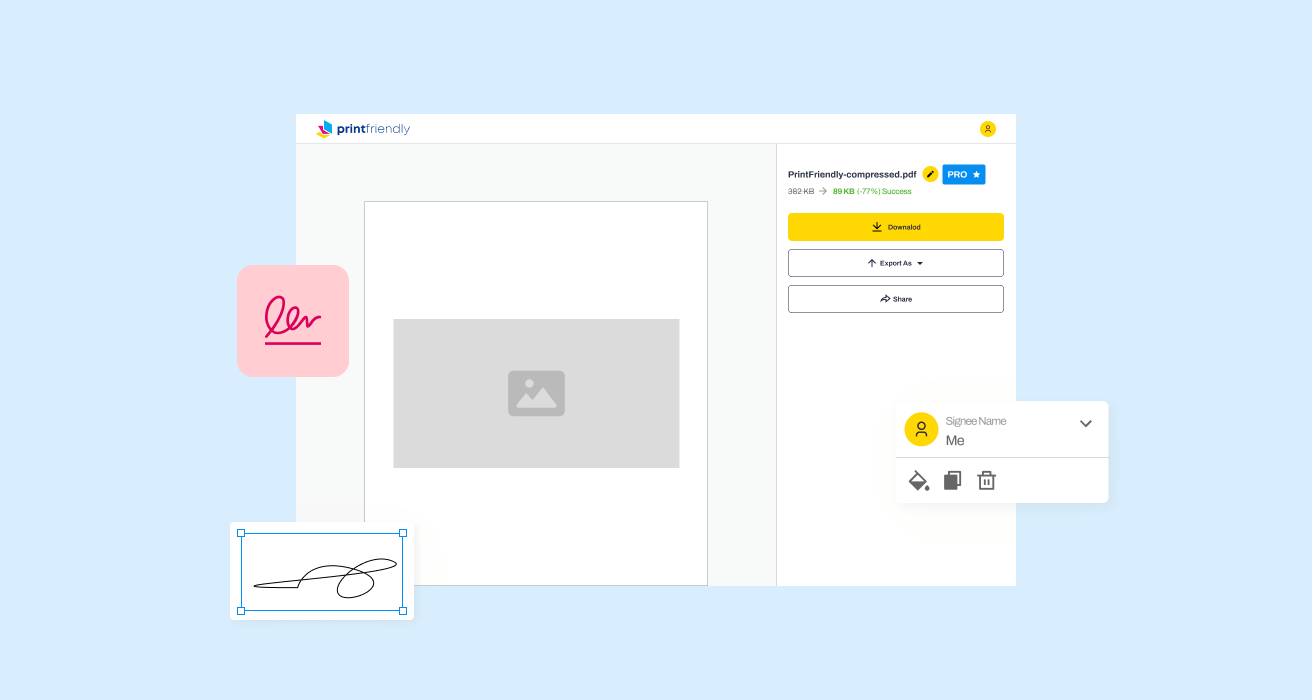
How to fill out the Implement Total Productive Maintenance (TPM) in Manufacturing Industry?
1
Analyze the current machine breakdown situation.
2
Apply Nakajima's seven steps of autonomous maintenance.
3
Implement various TPM pillars such as improvements, education, and training.
4
Measure Overall Equipment Effectiveness (OEE).
5
Apply the 5S methodology to maintain workplace organization.
Who needs the Implement Total Productive Maintenance (TPM) in Manufacturing Industry?
1
Manufacturing managers implementing TPM.
2
Maintenance engineers analyzing machine performance.
3
Quality control specialists interested in equipment effectiveness.
4
Industry researchers studying TPM methodologies.
5
Production technicians involved in autonomous maintenance.
How PrintFriendly Works
At PrintFriendly.com, you can edit, sign, share, and download the Implement Total Productive Maintenance (TPM) in Manufacturing Industry along with hundreds of thousands of other documents. Our platform helps you seamlessly edit PDFs and other documents online. You can edit our large library of pre-existing files and upload your own documents. Managing PDFs has never been easier.
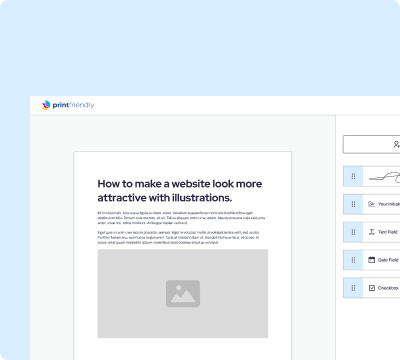
Edit your Implement Total Productive Maintenance (TPM) in Manufacturing Industry online.
With PrintFriendly, you can easily edit this PDF by adding your own data and annotations. Use our PDF editor tools to highlight important sections, make notes, and input your analysis. Save and download the edited document directly from PrintFriendly.
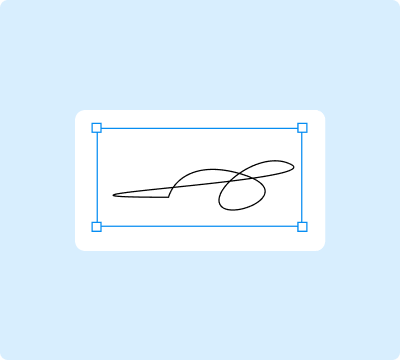
Add your legally-binding signature.
PrintFriendly allows you to sign PDFs easily with our integrated signature tool. Create and save your signature within the editor, then apply it to the document where needed. This ensures your completed file is authenticated and ready for submission.
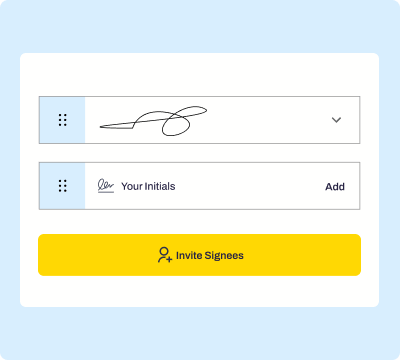
Share your form instantly.
Share your edited and completed PDFs through PrintFriendly by generating a shareable link or sending the document directly via email. Our sharing tools make it easy to collaborate and distribute important files securely. PrintFriendly ensures your documents are accessible to those who need them.
How do I edit the Implement Total Productive Maintenance (TPM) in Manufacturing Industry online?
With PrintFriendly, you can easily edit this PDF by adding your own data and annotations. Use our PDF editor tools to highlight important sections, make notes, and input your analysis. Save and download the edited document directly from PrintFriendly.
1
Upload the PDF file to PrintFriendly.
2
Open the PDF editor to input your data and analysis.
3
Use annotation tools to highlight and make notes.
4
Apply any necessary changes and review the document.
5
Save and download the edited PDF.
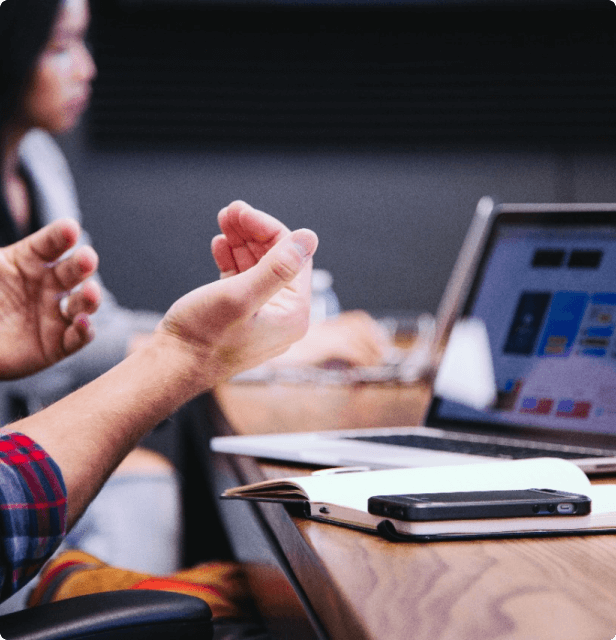
What are the instructions for submitting this form?
To submit this form, fill out all required information, including the analysis of current machine breakdowns, TPM implementation steps, and equipment effectiveness measurements. Once completed, you can submit the form via email to t.pra1008@gmail.com or patel_deep93@outlook.com. Alternatively, you can send it through a fax at [Fax Number] or use the online submission form available on [Website URL]. If necessary, you can mail the physical copy to the Parul Institute of Technology, Vadodara.
What is the purpose of this form?
The purpose of this form is to provide detailed guidelines and steps for implementing Total Productive Maintenance (TPM) in a manufacturing unit. TPM aims to reduce machine breakdowns, improve productivity, and maintain equipment in optimal condition. This form serves as a comprehensive resource for manufacturing professionals to enhance efficiency and effectiveness in their operations.
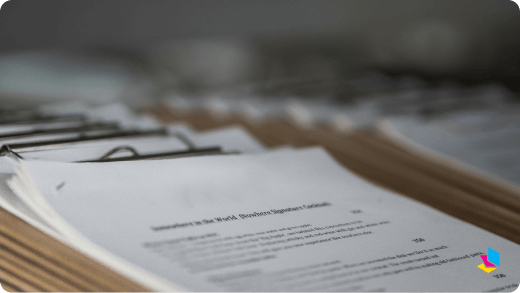
Tell me about this form and its components and fields line-by-line.

- 1. Title: The main title of the document.
- 2. Authors: Names and contact information of the authors.
- 3. Abstract: A summary of the study and its findings.
- 4. Keywords: Relevant terms associated with the content of the document.
- 5. Introduction: Overview of TPM and its significance in manufacturing.
- 6. Literature Review: Discussion of previous research and studies on TPM.
- 7. Case Study: Detailed analysis of the TPM implementation process.
- 8. Overall Equipment Effectiveness: Evaluation of equipment performance and effectiveness.
- 9. 5S Methodology: Description and application of the 5S steps.
What happens if I fail to submit this form?
Failure to submit this form may result in missed opportunities for improving equipment maintenance and productivity.
- Increased Machine Breakdowns: Without proper TPM, machines may experience more frequent breakdowns, leading to downtime and loss of productivity.
- Higher Maintenance Costs: Lack of structured maintenance practices can lead to higher costs due to emergency repairs and unplanned maintenance.
- Reduced Efficiency: Failure to implement TPM can result in lower overall equipment effectiveness, impacting production quality and output.
How do I know when to use this form?
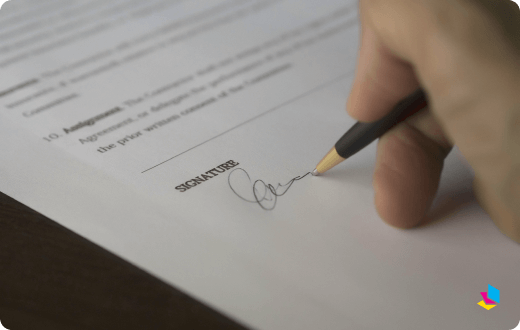
- 1. New TPM Initiatives: When starting a new TPM program, use this form to outline steps and guidelines.
- 2. Maintenance Improvements: Apply this form to analyze and enhance current maintenance strategies.
- 3. Equipment Effectiveness Measurement: Use this form to measure and track overall equipment effectiveness (OEE).
- 4. Training and Education: Utilize this form for training employees on TPM practices.
- 5. Continuous Improvement: Implement this form to ensure ongoing improvements and sustainability of TPM.
Frequently Asked Questions
Can I edit the PDF file directly on PrintFriendly?
Yes, you can use our PDF editor to make changes to the file directly.
How do I add my signature to the PDF?
Use the signature tool in our PDF editor to create and apply your signature.
Can I share the edited PDF with others?
Yes, you can create a shareable link or send the document via email using PrintFriendly.
What tools are available for editing?
Our editor includes tools for highlighting, annotating, and adding text or images.
How do I download the edited PDF?
Save your changes and click the download button to get the edited PDF file.
Can I collaborate with others on the same PDF?
Yes, you can share the document with collaborators and make joint edits.
Is there a limit to the number of edits I can make?
No, you can make as many edits as needed using PrintFriendly.
Will the formatting of the original PDF be preserved?
Yes, our editor ensures that the original formatting is maintained.
Can I edit the text within the PDF?
Yes, the PDF editor allows you to modify text within the document.
How do I access the PDF editor?
Upload your PDF to PrintFriendly and click on the 'Edit' button to access the editor.