AS9102 First Article Inspection Forms Overview
This document provides the AS9102 First Article Inspection forms from General Dynamics Ordnance and Tactical Systems. It includes detailed accountability and verification instructions for parts and processes relevant to manufacturing. Users can utilize this file for compliance and quality assurance in aerospace and defense manufacturing.
Edit, Download, and Sign the AS9102 First Article Inspection Forms Overview
Form
eSign
Add Annotation
Share Form
How do I fill this out?
Filling out these forms requires careful attention to detail to ensure all relevant information is accurately captured. Begin by collecting all necessary part and manufacturing information required by the AS9102 standards. Follow the instructions step-by-step to ensure each section is completed correctly.
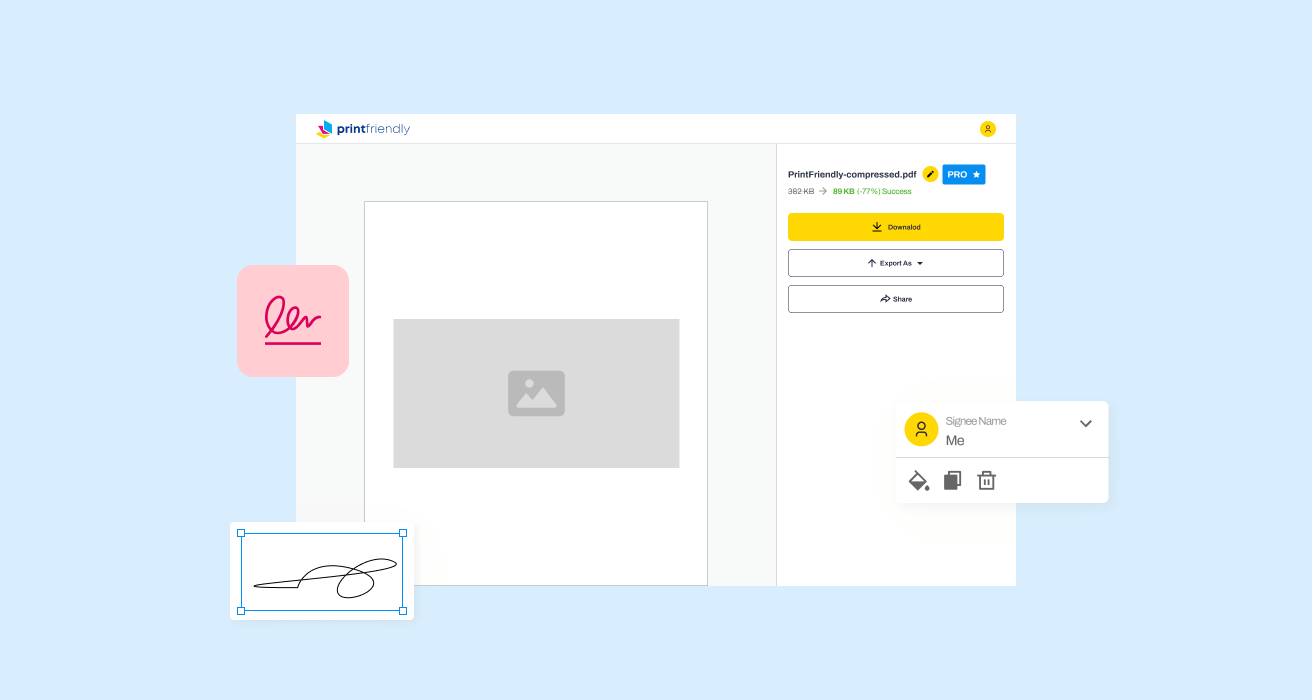
How to fill out the AS9102 First Article Inspection Forms Overview?
1
Gather all necessary information about the part and manufacturing process.
2
Fill out the required fields for part number, name, serial number, and inspection details.
3
Review each section for completeness and accuracy according to AS9102 standards.
4
Ensure signatures are provided where required to attest to the information.
5
Submit the completed form to the appropriate authority for review and approval.
Who needs the AS9102 First Article Inspection Forms Overview?
1
Quality Assurance professionals need this file to ensure compliance with aerospace standards.
2
Manufacturers require it for documenting first article inspections and process validation.
3
Suppliers use this form to provide accountability for parts and materials supplied.
4
Regulatory bodies need these forms for audits and inspections of manufacturing processes.
5
Project managers require this documentation for tracking progress and quality control.
How PrintFriendly Works
At PrintFriendly.com, you can edit, sign, share, and download the AS9102 First Article Inspection Forms Overview along with hundreds of thousands of other documents. Our platform helps you seamlessly edit PDFs and other documents online. You can edit our large library of pre-existing files and upload your own documents. Managing PDFs has never been easier.
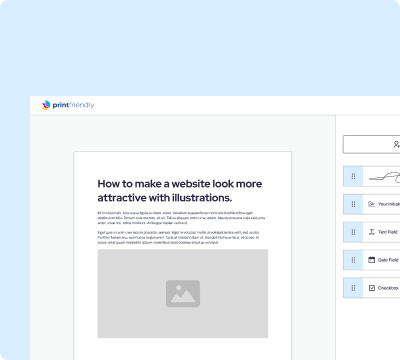
Edit your AS9102 First Article Inspection Forms Overview online.
You can easily edit this PDF on PrintFriendly by accessing the editing tools provided within the platform. This allows you to make changes directly on the PDF document, ensuring that all information is accurate and meets your requirements. Take advantage of the intuitive interface to enhance your editing experience.
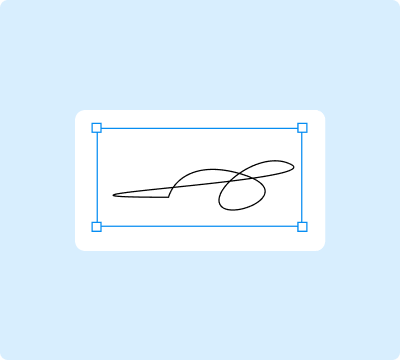
Add your legally-binding signature.
Signing the PDF is made simple on PrintFriendly with our integrated signature feature. Users can add their signatures directly to the document, ensuring authenticity and approval of the content. This streamlined process makes it easy to finalize your forms efficiently.
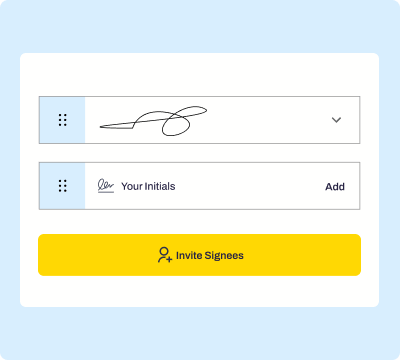
Share your form instantly.
Sharing the PDF from PrintFriendly is easy and effective with our new sharing options. You can easily send the document to colleagues or stakeholders via email or social media, facilitating collaboration. This feature ensures your files reach the intended audience quickly.
How do I edit the AS9102 First Article Inspection Forms Overview online?
You can easily edit this PDF on PrintFriendly by accessing the editing tools provided within the platform. This allows you to make changes directly on the PDF document, ensuring that all information is accurate and meets your requirements. Take advantage of the intuitive interface to enhance your editing experience.
1
Open the PDF document in PrintFriendly.
2
Use the editing tools to select and modify the text fields.
3
Add or remove any necessary components in the form.
4
Review all changes to ensure accuracy.
5
Download the edited file for your records.
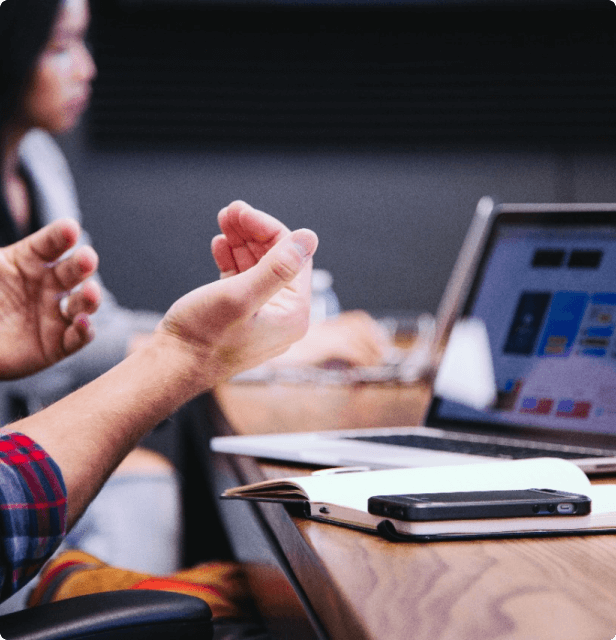
What are the instructions for submitting this form?
To submit this form, send it via email to the designated quality assurance department or fax it to the provided fax number. Ensure that all signatures are collected prior to submission for effective processing. It's recommended to maintain a copy of the submitted form for your records.
What are the important dates for this form in 2024 and 2025?
Key dates for AS9102 form submissions typically include production schedule deadlines and quality assurance review timelines. Ensure to check specific project timelines to align with these forms. It's crucial to adhere to these dates to maintain compliance and production efficiency.
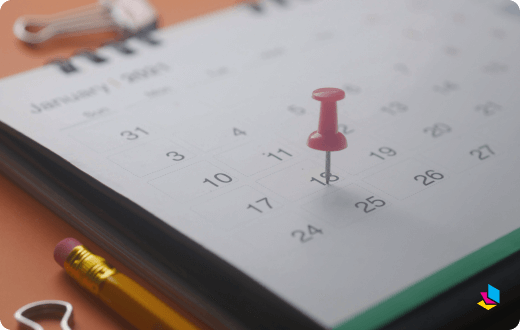
What is the purpose of this form?
The main purpose of these forms is to ensure that all first article inspections are conducted systematically and thoroughly. This documentation serves as a record for accountability in manufacturing, ensuring that all parts meet specified design and regulatory standards. Through proper use of these forms, organizations can uphold quality assurance and streamline production processes.
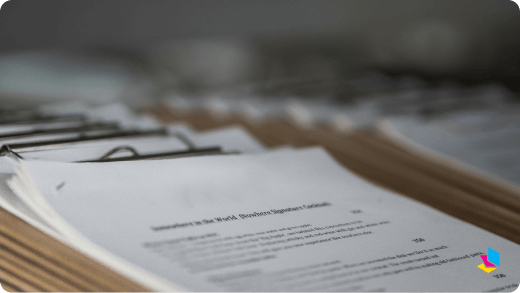
Tell me about this form and its components and fields line-by-line.

- 1. Part Number: Identifies the specific part being inspected.
- 2. Part Name: The name assigned to the part.
- 3. Serial Number: Unique identifier for each individual part.
- 4. Lot Number: Indicates the batch in which the part was produced.
- 5. FAI Report Number: Reference number for the first article inspection report.
- 6. Revision Level: Version of the part, capturing any updates or changes.
- 7. Drawing Number: Associated design document number for the part.
- 8. Supplier Code: Identifier for the supplier of the component.
- 9. Approval Signature: Signature of the individual approving the form.
What happens if I fail to submit this form?
Failure to submit this form may result in compliance issues and delays in production. It is vital to adhere to submission deadlines to ensure project continuity and quality assurance. Organizations may face audits or increased scrutiny during inspections if required documentation is missing.
- Compliance Risks: Non-compliance can lead to legal penalties and loss of credibility.
- Production Delays: Incomplete forms can halt production processes, impacting timelines.
- Quality Assurance Issues: Missing documentation can compromise quality checks and balances.
How do I know when to use this form?
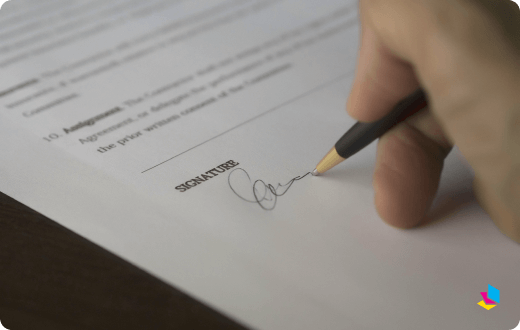
- 1. First Article Inspections: Whenever an initial inspection of a new part is conducted.
- 2. Routine Quality Checks: For regular compliance checks during production.
- 3. Supplier Accountability: When assessing supplier performance and part quality.
Frequently Asked Questions
What can I edit in this PDF?
You can edit text fields, add comments, and modify existing information within the document.
How do I download the edited PDF?
After making your edits, simply click the download button to save your changes.
Can I share this PDF with others?
Yes, you can share the PDF via email or social media directly from PrintFriendly.
What types of forms are included?
This file includes AS9102 First Article Inspection forms for various accountability purposes.
Is there a guide for filling out these forms?
Yes, the document includes instructions for completing each section accurately.
Who is responsible for completing the FAI forms?
Typically, quality assurance and manufacturing teams complete these forms.
What happens if the form is incomplete?
Incompleteness may result in processing delays or compliance issues.
How can I get assistance with this PDF?
You can reach out to our support team for help with any editing or downloading issues.
Are my edits saved automatically?
Currently, edits must be downloaded manually as changes are not saved automatically.
Is this PDF customizable?
Yes, you can customize the content to meet your specific needs before downloading.